AS -2
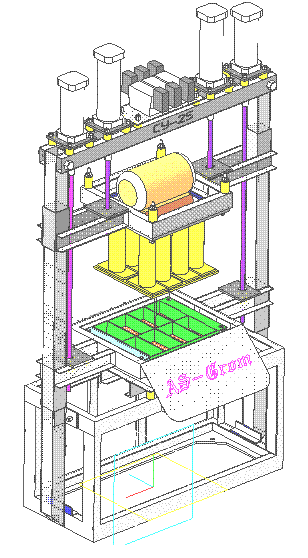
СУ-25, модель стационарной установки – АС-2пУ

ПАСПОРТ
вибропресса СУ-25 модель АС-2пУ
г. Ставрополь
2011 год.
Вариант АС-2пУ для Якова – осень.
СОДЕРЖАНИЕ
1. Введение
2. Назначение
3. Технические характеристики
4. Состав и комплектность
5. Устройство и принцип работы
6. Описание схемы электрической
7. Указание мер безопасности
8. Порядок транспортировки
9. Подготовка к работе
10. Порядок работы
11. Техническое обслуживание
12. Учет технического обслуживания
13. Свидетельство о приемке
14. Сведения о ремонте
Приложения:
1. Схема пневматическая принципиальная.
2. Схема электрическая принципиальная.
3. СВИДЕТЕЛЬСТВО О ПРИЕМКЕ ОБОРУДОВАНИЯ
4. Акт приёма-передачи оборудования.
При необходимости в дополнительной информации по продукции, а также при возникновении каких-либо вопросов обращайтесь - Владимир Николаевич, WNP@NM.ru 89188860060
1. ВВЕДЕНИЕ
Настоящий паспорт является объединенным документом, содержащим техническое описание, инструкцию по эксплуатации и паспорт на установку АС-2пУ по производству бетонных изделий. В связи с постоянной работой по совершенствованию комплекса, разработчик оставляет за собой право вносить изменения в конструкцию, не отраженные в паспорте.
2. НАЗНАЧЕНИЕ
«АС-2пУ» - стационарная установка, предназначенная для изготовления стеновых камней методом полусухого вибропрессования бетонных смесей. Исходными материалами для приготовления смеси служит заполнитель, вяжущее и вода. В качестве заполнителя могут использоваться песок, отсевы щебеночного производства, керамзит, шлаки и т.п. В качестве вяжущего применяют цемент. Применяемый способ получения изделий за счет принудительной расфасовки смеси в полости матрицы при одновременной двухсторонней вибрации позволяет извлекать качественно отформованные камни в количестве от 2-х штук через 17-48 секунд после загрузки смеси.
Установка может эксплуатироваться в закрытом помещении при температуре окружающего воздуха от +10º до +30ºС. В процессе работы установки камни выдавливаются из матрицы на поддоны. Готовые изделия подвергаются вылеживанию от 1 (при температуре +75С) до 3-х (при температуре +35С) суток с периодическим увлажнением, после чего они приобретают около 30% прочности и могут штабелироваться и транспортироваться. 100% прочности камни приобретают через 28 суток при температуре не менее +20С. При наличии у потребителя пропарочной камеры камни могут подвергаться тепловлажностной обработке. В этом случае заданную
прочность они приобретают после остывания и высыхания. Болтовое крепление комплекта "матрица-пуансон" позволяет производить замену этого комплекта для изготовления других строительных элементов. Дополнительный комплект "матрица-пуансон" может поставляться по специальному заказу.
3. ТЕХНИЧЕСКИЕ ХАРАКТЕРИСТИКИ
Общая масса от 350 кг
Напряжение питания / частота 380 В / 50 Гц
Установленная мощность от 0,515 кВт до 2,0 квт (по согласованию с заказчиком).
Время цикла формования 17...48 сек
Количество формовок за смену до 600 шт. Площадь формовки 0,4х0,4 м.
Количество одновременно формуемых шлакоблоков – 2 шт 390*190*188.
Обслуживающий персонал 1-2 чел.
Температура окружающей среды 5...45 с0
Привод матрицы, пуансона – пневматический, загрузка ручная, подача поддонов и съём с готовой продукцией – ручное.
Управление пневмооприводом ручное с системой блокировки от ошибочного включения, управление процессом производства полуавтоматическое циклическое с применением концевых выключателей и блока электромагнитных исполняющих элементов
Давление в пневмосистеме в среднем рабочее 0,6 МПа. Мин/макс 0,2/0,8 МПа МПа.
Тип компрессора может применяться в зависимости от условий требуемой производительности (Но не менее 250л/мин и ресивера от 100л – 1-2 шт.).
«ВНИМАНИЕ»
Установка поставляется без компрессора
1 - рама, 2. пуансон, 3 - пневмоцилиндры матрицы, 4 - цилиндры пуансона, 5 – матрица, 6 – направляющие, 9 – пульт управления (пневмораспределитель) с системой электромагнитной блокировки, 12 – компрессор (не входит в состав),

4. СОСТАВ И КОМПЛЕКТНОСТЬ
Комплект поставки:
- установка в сборе,
- пневмооборудование, установленное на АС-2пУ,
- электрооборудование, установленное на АС-2пУ,
Эксплуатационная документация:
данный паспорт и СД-диск с технической документацией.
5. УСТРОЙСТВО И ПРИНЦИП РАБОТЫ
Установка состоит из сварной рамы, матрицы и пуансона, рам-держателей матрицы и пуансона, вибростола с возможностью для изменения высоты разных поддонов, ручной загрузки бетонной смеси, электрообрудования, системой блокировки и полуавтоматического управления, цилиндры подъема - опускания матрицы, цилиндр подъема-опускания пуансона. Пуансон крепится на пуансонодержателе, связанном со штангами, которые соединены перемычкой. К щекам направляющих на 4-ти амортизаторах с каждой стороны крепится матрица и вибраторы.
Управление срабатыванием пневмоцилиндров матрицы и пуансона, осуществляется с пульта управления с системой блокировки от ошибочных действий оператора, которые могут привести к поломке механизмов, а также полуавтоматическое управление процессом цикла производства камней (с возможностью дополнительного применения поочередным включением вибраторов (верхнего и нижнего).
Нижний (и верхний) вибратор может быть подключен частотному регулятору позволяющему изменять частоту и амплитуду колебаний вибратора без механического вмешательства и дополнительно применить элементы динамического торможения двигателя. Последние элементы не входят в комплект и поставляются только дополнительно по согласованию с заказчиком.
5.1. Станция компрессорная
Станция предназначена для подачи рабочего газа – сжатого воздуха в исполнительные органы (цилиндры).
Тип станции зависит от условий договора поставки по согласованию с заказчиком.
5.2. Пульт управления электрический.
Пульт управления электрический предназначены для управления электродвигателями вибраторов и автоматики привода установки «АС-2пУ». Режим работы «ручной», «полуавтомат» или «автомат» зависит от условий поставки по согласованию с заказчиком.
Ручной режим управления – распределитель ручной, ручное кнопочное (или тумблерное) включение вибраторов, ручное механическое включение компрессора.
Полуавтоматический режим выбирается от условий поставки, распределитель может быть 2, 3 или 4-х секционный, система блокировки пневматики от ошибочных действий оператора, включение вибраторов электромагнитное автоматическое, блок сигнализации, блок электромагнитных элементов, концевые выключатели электромеханические, магнитные герконы или бесконтактные индуктивные (или емкостные, или оптические) выключатели. И до возможности применения контроллеров, программируемых реле и ТТР под спецзаказ по условию договора.
Автоматический режим применяется в случае подачи 100% гарантированной идеальной бетонной смеси. По согласованию с заказчиком управление может быть скомплектовано электронными компонентами (компьютер, датчики, элементы управления и привода) и поставляется со специальным (под заказчика) программным обеспечением.
Схема управления.
5.3 Работа установки
Установку обслуживает один оператор.
Исходное положение рабочих органов установки:
- пуансон находится в крайнем верхнем положении,
- матрица находится в крайнем нижнем положении,
- кнопки и выключатели в нейтральном положении.
Исходное положение пневмоцилиндров устанавливают вручную пилотными переключателями пневмораспределителей при выключенном питании управления.
Включение установки:
Включение компрессора и электрообрудования АС-2пУ автомат.выключателем (а также защита от перенапряжений и УЗО) на щите электрооборудования по месту установки у заказчика ( в комплект не входит).
Принцип работы:
Заполнять бетонной смесью в матрицу ручным способом.
Укладка смеси в матрицу производится методом вибродозирования, которое включается вручную (кратковременным включением ручного пускателя).
После виброукладки смеси в матрице начинают управление вибропрессом.
Пуансон опускается до касания смеси, начинается процесс вибропрессования до достижения формуемым изделием заданных размеров. При этом оператор включает вибродвигатели и держит для достижания требуемой высоты и уплотнения изделия. После этого начинается распалубка - матрица поднимается вверх до полного освобождения изделия. Затем поднимается пуансон и за ним матрица вверх. Вручную выдвигается поддон с готовой продукцией на приёмный стол (по условиям договора не входит в комплектацию). Последней завершающей операцией является включение кнопкой возврат матрицы (вниз) в исходное загрузочное положение.
5.3.1 Блокировки в полуавтоматическом и автоматическом режиме.
С целью увеличения производительности пресса применяется простейшая автоматизация процесса и его несложное кнопочное управление.
6. ОПИСАНИЕ РАБОТЫ СХЕМЫ ЭЛЕКТРИЧЕСКОЙ ПРИНЦИПИАЛЬНОЙ
Электрическая схема обеспечивает работу установки в рабочем режиме.
6.1 ПИТАНИЕ УСТАНОВКИ.
6.1.1 Питание (3 фазы 380 В 50 Гц 1500 ватт для вибраторов и 220 В 20 ватт для схемы управления) на электросхему управления установкой подается через автоматический выключатель и устройство защитного отключения (УЗО) по месте установки АС-2пУ от сети электропитания заказчика. При этом автоматический выключатель выполняет функцию защиты передвижной установки от токов короткого замыкания (сверхтоков), а устройство защитного отключения выполняет функцию защиты обслуживающего персонала от поражения электрическим током при прямом однополюсном прикосновении к токопроводящим частям установки и проводящим частям, которые могут оказаться под напряжением в случае повреждения изоляции. Дополнительно устройство защитного отключения обеспечивает защиту установки от токов короткого замыкания на землю и недопустимых токов утечки на землю. Согласно требованиям ПУЭ (Правил устройства электроустановок) в точке подключения электроустановки к источнику питания должно быть установлено устройство защиты от сверхтоков и устройство защитного отключения (УЗО), реагирующее на дифференциальный ток, номинальный отключающий дифференциальный ток которого должен быть на 1-2 ступени больше соответствующего тока УЗО, установленного на вводе в электроустановку. Установка устройства защиты от сверхтоков и устройства защитного отключения осуществляется потребителем. Присоединение установки АС-2пУ к контуру заземления обязательна, согласно ПУЭ и осуществляется потребителем.
6.1.2 При поступлении напряжения на установку должны быть приняты меры исключающие попадания на элементы электросхемы технических жидкостей и вредных веществ (пыли, грязи, воды, масла и т.п.)
7. УКАЗАНИЯ МЕР БЕЗОПАСНОСТИ
7.1. Эксплуатацию установки необходимо производить в соответствии с правилами пожарной безопасности, правилами работ с гидравлическим (пневматическом) прессовым оборудованием и общими правилами на погрузочно- разгрузочные работы (ГОСТ 12.1.004-85; ГОСТ 12.1.О12-78;ГОСТ 12.1.030-81; ГОСТ 12.3.О09-76). Меры безопасности при работе согласно правил работ с пневмооборудованием.
7.2. К работе на установке допускаются лица, ознакомившиеся с настоящей инструкцией по эксплуатации и имеющие опыт работы на подобном оборудовании.
7.2.1. Во время рабочего цикла лицо, управляющее органами установки, должно находиться в кресле оператора или отведенном рабочем месте стоя.
7.2.2. При работе не допускается нахождение посторонних предметов в рабочей зоне установки. Все ремонтные работы можно выполнять только на обесточенной установке. Выполнение работ с матрицей или пуансоном проводить после снятия их с установки.
7.2.3. При эксплуатации следует соблюдать общие правила электробезопасности для установок напряжением до 1000 в.
7.2.4. При изготовлении стеновых камней установку следует соединить гибким проводником сечением не менее 6 мм2 с существующим контуром заземления.
8. ПОРЯДОК ТРАНСПОРТИРОВКИ
Установка по производству стеновых камней транспортируется в вертикальном положении:
- матрица и пуансон находятся в нижнем положении
- пневмосистема и электросхема может быть снята с установки АС-2пУ,
- подводящие рукава и электрокабели отключены от установки АС-2пУ и компрессора,
9. ПОДГОТОВКА К РАБОТЕ
9.1. Установить и закрепить установку АС-2пУ на анкера 10 гайками 11 в фундаменте (приямки 300х300хh500) через жесткие демпферные подушки 12 (траспорт.лента 7-10мм) для гашения излишков вибрации.

9.2. Перед пуском установки необходимо проверить фильтр-регулятор.
«ВНИМАНИЕ»
При отсутствии фильтра или его неисправности работа установки недопустима.
9.2.1. Проверить отсутствие внешних повреждений рукавов, цилиндров, электроприводов, электрокабеля, конечных выключателей и надежность крепления резьбовых соединений.
9.2.6.1. Установить рукоятками распределителя поочередно:
пуансон в верхнее исходное положение,
матрицу в нижнее исходное положение,
«ВНИМАНИЕ»
КАТЕГОРИЧЕСКИ ЗАПРЕЩЕНО ПЕРЕМЕЩАТЬ РУКОЯТКИ УПРАВЛЕНИЯ ВО ВРЕМЯ ОСМОТРА КОНЦЕВЫХ ВЫКЛЮЧАТЕЛЕЙ!
9.2.6.3. Установить рукоятками пульта управления поочередно:
матрицу – вверх,
пуансон - в матрицу вниз,
И т.д.
9.2.6.4. Настройку электронной полуавтоматики и выключателей конечных (в дальнейшем ВК) производить с учетом электросхемы и конструктивных особенностей при перестановки матриц и техническом обслуживании. в части исходного положения. Настройку момента срабатывания ВК производить перемещением их в горизонтальной и вертикальной плоскостях с последующей фиксацией. С целью обеспечения блокировки должны срабатывать в пределах 5...7 мм до крайнего положения. Порог включения и отключения ВК вибраторов можно изменять в пределах 10...50 мм в зависимости от технологии вибропрессования различных смесей.
Недопустима настройка ВК при работающем компрессоре.
10. ПОРЯДОК РАБОТЫ
10.1. Работа электроприводов от пульта управления в наладочном режиме. Электросхема включена в сеть.
10.1.1. Привести в исходное положение цилиндров (кнопками или «пилотами»).
10.1.2. Включить АВ входной, пуск компрессора и питание электрооборудования.
10.1. Установить рукоятками пульта управления.
10.2. Работа в полуавтоматическом режиме.
10.2.1.. Заполнить матрицу рабочей смесью и предварительно отвибрировав смесь нижним вибратором от 0,5 до 2 секунд.
10.2.2. Опустить пуансон на матрицу и произвести прессование с единовременным включением обеих вибраторов (если установлены).
10.2.3. Поднять матрицу и потом поднять пуансон.
10.1.10. И снять поддон с готовой продукцией.
10.1.11. Произвести возврат матрицы вниз.
10.3. Работа электроприводов и оборудования в автоматическом режиме - согласно требованиям технологии производства и конструкции установки АС-2пУ.
10.4. Характерные неисправности и методы их устранения.
Не работает – проверить состояние ВК и блока электромагнитов (реле, пускателей, контакторов), отрегулировать концевые положения, проверить надёжность электрических соединений.
Не срабатывает автоматическое включение электровибраторов– проверить состояние ВК пуска вибраторов и блока электромагнитов (реле, пускателей, контакторов), отрегулировать концевые положения, проверить надёжность электрических соединений.
11. ТЕХНИЧЕСКОЕ ОБСЛУЖИВАНИЕ
11.7.1. Смазку подвижных соединений установки производить своевременно.
11.7.3. Следить за зазором между матрицей и пуансоном.
11.7.4. Периодически проводить проверку затяжки всех резьбовых соединений. При необходимости произвести подтяжку и контровку. Следить за состоянием необходимых зазоров (касания гроверов и просвета держателей).
11.7.5. Для нормального функционирования установки необходимо после работы очищать матрицу, пуансон, дозатор, и бункер от остатков смеси.
11.7.6. Перед началом работы установки смазать рабочие поверхности матрицы, пуансона, дозатора и бункера заполняемые смесью, (автолом) или моторным отработанным. Хорошие результаты смазки показало применение крема для рук «Oriflame».
11.8.Съем и установка матрицы и пуансона.
Производятся бригадой не менее двух человек согласно конструкции с применением механизмов и средств исключающих падение и нанесение травм персоналу.
11.8.6. Порядок регулировки зазора между матрицей и пуансоном:
а) опустить матрицу в крайнее нижнее положение
б) ввести пуансон в матрицу (32мм) для обеспечения требуемой высоты изделий.
в) ослабить болты крепления пуансона к пуансонодержателю
г) включить вибраторы матрицы на 3…5 сек.
д) затянуть болты до момента касания гроверов болтов крепления пуансона к пуансонодержателю.
11.8.7. Регулировки вибростола, креплений матрицы и цилиндров производить по мере необходимости, но при постоянном контроле со стороны оператора установки и ежедневного контроля ответственного за производство и установку лица.
ПРИМЕЧАНИЕ.
* С целью улучшения производительности и повышения надежности оборудования, Производитель оставляет за собой право изменять конструкцию оборудования без уведомления Заказчика
** Указанные технические характеристики являются приблизительными и могут изменяться в зависимости от вида изготавливаемого изделия и качества сырья
Дополнения и изменения внесенные в конструкцию по просьбе заказчика:
- Увеличенный ход пуансона с 250 до 450 мм, то есть почти в ДВА РАЗА, это сделано для удобства загрузки смеси,
- увеличенный запас мощности пневмоцилиндров с 80 до 100, то есть по объёму почти в ДВА РАЗА, как то просил клиент;
- простая схема полуавтоматического управления пневматикой;
- ручное управление вибродвигателями для обеспечения выполнений технологий при производстве различных бетонных изделий по высоте, плотности, влажности и пластичности.
- простая и легкоремонтогодная система и электросхема управления вибраторами;
- возможность установки вибраторов согласно требуемой технологии;
- предусмотрено крепление и установка доп.вибраторов на пуансоне;
- предусмотрено в конструкции доп.кнопка для дальней комплектации пресса системой выталкивания поддонов;
ПРИМЕЧАНИЕ.
Принципиальные cхемы, измененные по просьбе заказчика, прилагаются к данному паспорту дополнительно.
* С целью улучшения производительности и повышения надежности оборудования, Производитель оставляет за собой право изменять конструкцию оборудования без уведомления Заказчика
** Указанные технические характеристики являются приблизительными и могут изменяться в зависимости от вида изготавливаемого изделия и качества сырья
*** Возможны изменения в отдельных узлах конструкции станка, которые не влияют на требования ГОСТа и ПУЭ, и не ухудшают качество выпускаемой продукции.
Гарантийные обязательства Производителя не распространяются на оборудование, в котором нарушены заводские настройки или каким-либо образом была изменена конструкция.
ТЕХНОЛОГИЯ ИЗГОТОВЛЕНИЯ СТЕНОВЫХ КАМНЕЙ
В основу работы установки положен метод полусухого вибропрессования. В качестве сырья используется бетонная смесь, состоящая из трех основных частей: связующее, заполнитель и вода.
Свежее связующее, правильный выбор заполнителя и размера его зерен гарантирует получение бетонной смеси требуемого качества, а применение очищенной воды - важное условие производства однородных камней высокого качества.
В качестве связующего, используется цемент. Для изготовления камней применяется портландцемент или шлакопортландцемент марки 400. Для этой марки цемента осуществлен подбор составов, приведенных ниже.
При использовании цемента марки 300 его расход необходимо увеличить на 15%.
В качестве заполнителя используется песок, щебень, шлаки, керамзит, золы, опилки, гранулы полистирола и другие заполнители, а также их любые комбинации.
Заполнители не должны содержать чрезмерное количество пыли, мягких, глинистых и пластичных включений. Заполнители подразделяются на два вида: мелкие и крупные. Мелкие заполнители - песок кварцевый, отходы щебеночного производства - мелкие частицы гранита, доломита, мрамора и т. д., мелкие доменные шлаки.
Мелкий заполнитель обеспечивает пластичность смеси и стенового камня и образует его более гладкую поверхность. Избыток мелкого заполнителя снижает прочность бетона.
Крупные заполнители - материалы, имеющие зерна размером 5 мм и больше. Максимальный размер зерен ограничен размерами формуемого камня и не должен превышать 1/3 от наименьшего линейного размера камня. При минимальной толщине стенок и перемычек камней, полученных на установке равной 30 мм, максимальный размер зерен составляет 10 мм. При увеличении размера зерен появляется вероятность их заклинивания в матрице установки.
Для производства стеновых камней используется так же большая группа легких заполнителей (относящихся к крупным). Бетон считается легким, если его 1 куб.м весит менее 1800 кг.
Вода, используемая для приготовления смеси, не должна содержать примесей масел, кислот, щелочей, органических веществ; Вода служит не только для улучшения формования камней, но и играет определяющую роль в гидратации (схватывании) цемента. Любые примеси в воде снижают прочность камней и могут вызвать нежелательное преждевременное и замедленное схватывание цемента. Температура воды не должна быть ниже 15 С. Снижение температуры ведет к увеличению времени схватывания бетона. Вода для приготовления бетонных смесей должна удовлетворять требованиям ГОСТ 23732.
Химические добавки - используются для снижения количества цемента, увеличения скорости его схватывания, сокращения продолжительности тепловлажностной обработки изделий, придания бетону способности твердеть в зимнее время, повышения его прочности и морозостойкости.
Для ускорения твердения применяется хлористый кальций CaCl2. Количество добавок хлористого кальция составляет 1...3% от массы цемента. Эти добавки повышают прочность бетона в возрасте трех суток в 2...4 раза, а к 28 суткам прочность оказывается такой же, как у бетона без добавок.
СОСТАВ БЕТОНОВ: Состав смесей подбирается из назначения камня. Влиять на свойства получаемой продукции можно, главным образом, путём выбора соотношения мелкого и крупного заполнителя и изменения пропорции между общим количеством заполнителя и вяжущего. Состав смеси, обеспечивающей максимальные теплоизоляционные свойства, не гарантирует наилучших прочностных и влагопоглощающих характеристик камней. Поэтому соотношение крупного и мелкого заполнителя, пропорция между заполнителем и вяжущим обычно являются компромиссом, которым изготовитель добивается наиболее важных для него характеристик камней.
Материалы для приготовления бетонных камней (заполнители, вяжущие, добавки) должны удовлетворять требованиям соответствующих стандартов. Контроль за качеством поступающих материалов и их испытания должны осуществляться строительной лабораторией Заполнители (ГОСТ 9757-83), песок плотный и пористый природный, дробленый из отходов дробления (ГОСТ 8736-85, 22263-76, 25137-82), золошлаковые отходы (ГОСТ 25592-85, 25818-83 и т.п.).
Содержание пылевидных частиц в заполнителях (фракции менее 0,14 мм, как правило не должно превышать 10%). Это достигается промывкой заполнителя. Промывка заполнителя дает увеличение марки получаемого камня до 20% при том же расходе цемента.
Складировать и хранить крупные и мелкие заполнители необходимо раздельно по фракциям в условиях, исключающих засорение и смешивание, а также увлажнение.
Хранение цемента должно быть в стационарных или передвижных складах (силосах), в специальных контейнерах, имеющих устройства для его приема и выдачи.
КОЛИЧЕСТВО ВОДЫ И СМЕСИ.
При изготовлении камней методом полусухого вибропрессования бетонная смесь требует гораздо меньше воды, чем при обычной заливке бетона в формы. Избыток воды образует в бетоне множество тонких капиллярных пор и полостей. Для полного прохождения реакции схватывания достаточно всего 15...20% воды от массы цемента. Бетонная смесь с таким содержанием воды является почти сухой.
Однако почти сухую смесь трудно качественно перемешать, отформованные из нее камни осыпаются при выпрессовке из матрицы. Избыток воды также оказывает отрицательное воздействие на процесс изготовления камней.
Оптимальным является такое количество воды в смеси, при котором в конце процесса прессования из зазоров между пуансоном и матрицей и между матрицей и полом (поддоном) начинает появляться небольшое количество цементного молока.
Опытные операторы обычно легко оценивают качество смеси путем сильного сжатия её в руке. Если при этом получается нерассыпающийся плотный комок без выступающей влаги и при затирании его поверхности гладким металлическим предметом получается гладкая блестящая, влажная поверхность, то количество воды подобрано правильно.
ПЕРЕМЕШИВАНИЕ СМЕСИ
Продолжительность перемешивания смеси играет важную роль в получении прочного камня. Цель перемешивания состоит в покрытии каждой частицы заполнителя вяжущим. Мощный смеситель принудительного действия, которым может быть оснащена установка, обеспечивает высокую скорость и равномерность перемешивания, за счет подведения к каждой частице смеси большой энергии.
Гравитационные бетоносмесители не обеспечивают должного перемешивания жесткой смеси. Ручное перемешивание вообще неприемлемо.
ИСПЫТАНИЯ БЕТОННОЙ СМЕСИ
Точные и окончательные результаты подбора смеси могут быть получены только лабораторным путем.
Исследование образцов бетонной смеси осуществляется лабораториями испытаний строительных материалов, которыми оснащены практически все средние и крупные бетонные узлы и заводы.
Объем и методы лабораторных испытаний бетонной смеси описаны в ГОСТах:
- ГОСТ 10191.0-91 "Смеси бетонные. Общие требования к
методам испытаний",
- ГОСТ 12730.1-78 "Бетоны. Методы определения плотности";
- ГОСТ 12730.2-78 "Бетоны. Методы определения влажности";
- ГОСТ 10060-87 "Бетоны. Методы определения морозостойкости";
- ГОСТ 8462-85 "Материалы стеновые. Методы определения прочности при сжатии и изгибе".
Установка "" обеспечивает лишь формование камней, служит совершенной опалубкой для придания бетону требуемой формы. Прочность, морозостойкость и другие свойства камней зависят от того, какой бетон использован для их приготовления. Высокопрочный бетон обеспечит высокую прочность и морозостойкость камней и наоборот, бетон из старого цемента и грязного (не промытого) мелкого заполнителя дает низкое качество камней, независимо от конструкции средства для их формования.
Технические требования к камням даны в ГОСТ 6133-84 "Камни бетонные стеновые", который является основным руководящим документом для изготовления камней.
СОСТАВ БЕТОНОВ ДЛЯ ИЗГОТОВЛЕНИЯ СТЕНОВЫХ КАМНЕЙ
Подбор составов осуществлен на портландцементе марки 400. При использовании цемента марки 300 расход цемента следует увеличить на 15%. При необходимости повысить прочность камня на 10 кгс/см2 (например, с марки 40 до марки 50) расход цемента в бетоне следует увеличить на 10...15%.
СОСТАВЫ БЕТОННЫХ СМЕСЕЙ ДЛЯ ПРОИЗВОДСТВА ТРОТУАРНОЙ ПЛИТКИ; БОРДЮРНЫХ КАМНЕЙ И Т.П.
При производстве тротуарных плит необходимо руководствоваться ГОСТ 17608-81.
Тротуарные плиты должны изготовляться из тяжелого бетона марок МЗОО, М350, М400, М450. Из песчаного бетона марки не менее 400.
Для приготовления рабочей смеси бетона в качестве мелкого заполнителя следует применять кварцевые пески или дробленые пески, соответствующие требованиям ГОСТ 10268 - 80. Модуль крупности песка, применяемого для изготовления плит из песчаного бетона, должен быть не менее 2,6.
В качестве крупного заполнителя следует применять щебень из естественного камня или щебень из гравия ГОСТ 10268-80, а также щебень из доменного шлака по ГОСТ 5578-76.
Наибольшая крупность заполнителя (щебня) для бетона тротуарных плит толщиной более 50 мм не должна превышать 10 мм.
Вода для затвердевания бетонной смеси должна отвечать требованиям ГОСТ 23732-79.
При тепловлажностной обработке отформованных тротуарных плит из тяжелого песчаного бетона должны применяться мягкие режимы твердения (не выше + 65 С).
ПРИМЕЧАНИЕ.
* С целью улучшения производительности и повышения надежности оборудования, Производитель оставляет за собой право изменять конструкцию оборудования без уведомления Заказчика
** Указанные технические характеристики являются приблизительными и могут изменяться в зависимости от вида изготавливаемого изделия и качества сырья
*** Возможны изменения в отдельных узлах конструкции станка, которые не влияют на требования ГОСТа и ПУЭ, и не ухудшают качество выпускаемой продукции.
Гарантийные обязательства Производителя не распространяются на оборудование, в котором нарушены заводские настройки или каким-либо образом была изменена конструкция.
ДОПОЛНЕНИЕ К ПАСПОРТУ от 19 09 2011г.
Монтаж, подготовка к первоначальному пуску и пуск установки.
Установка монтируется на виброизолированном фундаменте в соответствии со схемой приведенной на рис. 1. План фундамента и координаты фундаментных болтов показаны на рис. 13.
Прежде, чем начать монтаж установки, необходимо выполнить виброизолированный фундамент по схеме приведенной на рис. 5. Работать на вибропрессе можно только после того, как фундамент наберет 100% прочности (28 дней при температуре 20 ºС и 100% влажности).
Монтаж установки начинается с установки пресса на рабочем месте.
Подсоединить компрессорную установку к вибропрессу в соответствии со схемой пневматической. Отрегулировать давление от 3 до 7 бар.
Выполнить электромонтажные работы в соответствии со схемой.
Включить компрессорную установку и опробовать работу установки на холостом режиме. Проверить герметичность соединений пневмотрубопроводов.
Рис. 5. План фундамента.

4. Работа установки.
Исходное состояние установки: к электрошкафу и смесителю подведено напряжение, автоматический выключатель включен, компоненты бетонной смеси подготовлены к загрузке смесителя, компрессорная установка включена, матрица и пуансон вибропресса находятся в верхнем положении.
В работе установки непосредственно участвуют один оператор и один или два подсобных рабочих. Подсобный рабочий № 1 загружает компоненты бетонной смеси в смеситель, включает смеситель, готовит бетонную смесь, загружает смесь в фартук матрицы. Оператор разравнивает смесь в матрице, оперируя кнопками пульта управления производит формовку камней, перемещает поддон с камнями из зоны формования на приёмный стол, вместе с подсобным рабочим перемещает поддон с готовыми камнями с него на стеллаж. Подсобный рабочий №2 вместе с оператором перемещает поддон с готовыми камнями со стола на стеллаж, устанавливает пустой поддон в зону формования, с помощью грузоподъемного устройства перемещает стеллаж наполненный поддонами в зону вылеживания или пропарку.
Порядок работы на установке следующий:
Подсобный рабочий № 2 устанавливает поддон в зону формования.
Оператор, манипулируя кнопками пульта, опускает матрицу в крайнее нижнее положение, на поддон.
Подсобный рабочий № 1 загружает компоненты смеси в смеситель, включает его, готовит смесь и по ее готовности загружает необходимое количество смеси в матрицу.
Оператор, кратковременно включает вибратор для предварительной виброукладки, разравнивает и уплотняет смесь в матрице, убирает излишки смеси, опускает пуансон и производит формование одновременно включая нижний вибратор и перемещая пуансон вниз. Необходимый размер камня по высоте обеспечивается, тогда пуансон достиг крайнего нижнего положения, но только в том случае, когда пуансон уже не оказывает давления на изделие.
Верхние вибраторы могут включатся автоматически, а включение нижнего вибратора обеспечивает только оператор вручную, благодаря подбору опытным путём времени включения.
Необходимо отметить, что степень уплотнения и высота изделия напрямую зависят от длительности включения вибратора при загрузке смеси в матрицу. Длительность включения при загрузке матрицы необходимо подбирать с таким расчетом, чтобы длительность включения вибратора при формовке была в пределах 0,3…2,0 с предвибрации при заполнении матрицы и до 15 с при окончательной формовке. Все временные параметры в большой степени зависят от жесткости смеси и характера заполнителя и подбираются экспериментально.
Не отрывая пуансон в первоначальный момент от свежеотформованных изделий, оператор поднимает матрицу вверх или автоматически. Происходит распалубка изделий непосредственно на поддоне. После освобождении всей боковой поверхности изделий поднимает пуансон вверх, оставляя готовое изделие на поддоне. Подсобный рабочий №2 выталкивает поддон с готовыми камнями из под матрицы на стол и вместе с оператором переносят поддон с отформованными изделиями на стеллаж. Подсобный рабочий №2 устанавливает пустой поддон в зону формования и цикл повторяется.
В случае, если на установке работают два человека, обязанности подсобного рабочего №2 выполняют оператор и подсобный рабочий №1.
Подбор состава бетонной смеси
В настоящее время во всех районах России и СНГ успешно работают около 50 линий СУ-25 и АС-2 и на каждой из них был без труда пройден этап поиска состава смеси. Этот этап занимает обычно около одного – двух – трёх месяцев. По истечении этого времени изготовители изделий начинают достаточно уверенно ориентироваться в деталях производства и потребностях местного строительного рынка.
Количество воды в смеси
При изготовлении изделий методом вибропрессования бетонная смесь требует гораздо меньше воды, чем при обычной заливке бетона в формы. Известно, что слишком большое количество воды в бетоне уменьшает его прочность. Для полного прохождения реакции схватывания достаточно всего 15...20% воды от массы цемента.
Бетонная смесь с таким содержанием воды является почти сухой. Метод вибропрессования позволяет применять смеси с минимальным количеством воды, так как заполнение матрицы происходит за счет вибрации и давления на смесь, а не за счет текучести смеси, как в обычном жидком бетоне.
При перемешивании недостаточно влажной смеси частицы вяжущего плохо прилипают к частицам заполнителя, отформованные из слишком сухой смеси изделия осыпаются при выпрессовке из матрицы или в них появляются трещины. Избыток воды также оказывает отрицательное воздействие на процесс изготовления изделий. Переувлажненная смесь становится слишком липкой. Это затрудняет заполнение матрицы вибропресса и вызывает разрушение верхней плоскости отформованных изделий из-за прилипания смеси к пуансону при его подъеме. Кроме того, выпрессованные изделия оплывают на поддоне, приобретая бочкообразную форму и теряют точность размеров.
При изготовлении стеновых камней оптимальным является такое количество воды в смеси, при котором поверхность выпрессованных из матрицы камней имеет сухой вид, но при перемещении поддонов от стола вибропресса к стеллажу накопителя в изделиях не появляются трещины.
Опытные операторы обычно легко оценивают качество смеси для всех изделий визуально, по ее внешнему виду в работающем смесителе. При освоении оборудования оператор смесителя может останавливать его для оценки влажности смеси на ощупь, путем сильного сжатия ее в руке. Если при этом получается не рассыпающийся плотный комок без выступающей влаги и при затирании его поверхности каким-либо гладким металлическим предметом получается гладкая, блестящая, влажная поверхность, то количество воды подобрано правильно.
Продолжительность перемешивания смеси.
Перемешивание смеси играет важную роль в получении прочного бетона. Цель перемешивания состоит в покрытии каждой частицы заполнителя тонкой пленкой вяжущего. Время перемешивания смеси на смесителе линии не должно быть меньше 1 минуты.
Особенности изготовления отдельных видов изделий.
Полнотелые стеновые камни.
Из всех изделий, которые могут изготавливаться на оборудовании СУ-25 (модель АС-2пУ) производство полнотелых камней является наиболее простым и осваивается за минимальное время. Это объясняется тем, что матрица полнотелых камней не имеет пустотообразователей и легко заполняется бетонной смесью. К смеси могут не предъявляться какие-либо повышенные требования: она может иметь относительно широкие колебания влажности и приготавливаться из низкосортного цемента и заполнителя фракцией до 15 мм. Отсутствие пустот в камне обеспечивает ему повышенную прочность в процессе выпрессовки и транспортировки сырых камней, что позволяет даже операторам с минимальным опытом получать качественные камни. Отсутствие пустот обеспечивает камням повышенную прочность и после созревания, поэтому у покупателей редко возникают претензии к их прочности
Пустотелые и перегородочные стеновые камни.
Изготовление этих камней также не сложно и легко освоено всеми потребителями оборудования СУ-25 (модель АС-2пУ). По сравнению с полнотелыми камнями пустотелые требуют несколько более тщательного подбора смеси по фракциям. Максимальный размер зерен крупной фракции бетонной смеси не должен превышать 1/3 минимальной толщины стенки камня.
Бортовые камни.
Несмотря на простую форму матрицы, позволяющую осуществлять ее быстрое заполнение смесью, производство бортовых камней является одним из самых сложных. Эта сложность объясняется высокими требованиями к внешнему виду и прочности бортовых камней. Для исключения трещин при формовании и получения высокой прочности после созревания бетона при изготовлении бортовых камней необходимо использовать смесь с тщательно подобранным фракционным составом. Повышенное содержание пылевидной фракции, облегчающей выпрессовку и транспортировку сырых изделий, при производстве бортовых камней также увеличивает количество брака из-за прилипания смеси к пуансону. Кроме того, для получения внешней поверхности удовлетворительного качества в бетонной смеси для этих изделий недопустимо присутствие частиц заполнителя крупнее 5 мм.
Наилучшие результаты при изготовлении бортовых камней достигаются при использовании в качестве заполнителя песка.
Тротуарная плитка.
Изготовление тротуарной плитки является наиболее ответственным среди всех изделий, которые могут производиться на оборудовании СУ-25 (модель АС-2пУ). Лучшим заполнителем для изготовления плитки является песок. Наличие зерен крупнее 3 мм нежелательно, т.к. они вызывают появление на верхней поверхности плитки крупных пор и углублений.
Плитки могут окрашиваться путем введения светостойких красителей в бетонную смесь во время её перемешивания. Количество красителя зависит от насыщенности цвета и состояния поставки красителя.
Испытание изделий и документальное подтверждение их качества.
Говоря о прочности изделий, получаемых на оборудовании АС-2пУ необходимо понимать, что это оборудование служит лишь совершенной опалубкой для придания бетону необходимой формы. Прочность, морозостойкость и другие свойства изделий на 90% зависят от того, какой бетон использован для их приготовления. Высокопрочный бетон с воздухововлекающими добавками обеспечит высокую прочность и морозостойкость изделий и наоборот, бетон из старого цемента и грязного мелкого заполнителя обусловит низкое качество изделий независимо от конструкции вибропресса.
Объективную информацию о действительных характеристиках изделий могут дать только испытания, которые осуществляют лаборатории испытаний строительных материалов при бетонных узлах и заводах или другие учреждения, имеющие технические возможности и полномочия для проведения испытаний. Полученные в результате испытаний официальные документы о прочности, морозостойкости, уровне поглощения влаги и других характеристиках изделий позволяют изготовителю гарантировать качество реализуемой продукции, а потребителю на основании этих документов рассчитывать этажность зданий, толщину стен, необходимость их влаго- и теплоизоляции.
Технические требования к отклонению размеров стеновых камней, их внешнему виду, наличию пятен, раковин и наплывов, требования к отпускной прочности, правила приемки, все необходимые виды и методы испытаний, требования к маркировке, хранению, транспортированию камней и гарантии изготовителя описаны в ГОСТ 6133-99 “Камни бетонные стеновые”, который является основным руководящим документам для изготовителя камней.
В связи с постоянной работой по совершенствованию оборудования, разработчик оставляет за собой право вносить изменения в конструкцию, не отраженные в паспорте.
ПРОИЗВОДИТЕЛЬ оборудования АС-2пУ гарантирует его работоспособность при соблюдении потребителем требуемых условий ПУЭ, ПТБ, хранения, транспортировки и эксплуатации. Гарантийный срок эксплуатации – 12 месяцев, согласно принятых норм изготовителя
Изготовитель гарантирует работоспособность установки при соблюдении потребителем требуемых условий хранения, транспортировки и эксплуатации. Гарантийный срок эксплуатации – 12 месяцев. Предъявление претензий к изготовителю возможно только в течении первой недели эксплуатации, но не позже одного месяца после приёмки (отгрузки) оборудования, при условии соблюдении технических требований. В случае самовольного изменения в конструкции со стороны заказчика-эксплуатационника и других нарушений правил эксплуатации производитель не несёт ответственность по гарантийному обслуживанию.
Начало гарантийного срока эксплуатации исчисляется со дня отгрузки установки. При решении спорных вопросов стороны руководствуются “Приложением о поставке продукции производственно-технического назначения ”утв. Постановлением СМ СССР от 25.07.88г.№888.
ПРИМЕЧАНИЕ.
* С целью улучшения производительности и повышения надежности оборудования, Производитель оставляет за собой право изменять конструкцию оборудования без уведомления Заказчика
** Указанные технические характеристики являются приблизительными и могут изменяться в зависимости от вида изготавливаемого изделия и качества сырья
